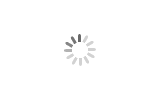
Automotive Prototype Rapid Injection Mold
Product origin China
Delivery time as customer requested
Supply capacity as customer requested
Part name: Automotive Prototype Rapid Injection Mold
Material: steel, P20 (1.2311), H13 (1.2344), S136 (1.2083), NAK80 (P21), 718 (1.2738), 420 (1.2083),420 (1.2083) etc.
Mould type: Prototype Rapid mold
Cavity&Core: steel, P20 (1.2311), H13 (1.2344), S136 (1.2083), NAK80 (P21), 718 (1.2738), 420 (1.2083),420 (1.2083) etc.
Mould base: LKM
Hot runner: needle nozzle direct on part, hot tip, etc.
Cold runner:tunnel gate
Tolerance: 0.05mm
Charactristic: Cost-effective, Design flexibility, material selection, Consistency and quality, Time and resource savings
1. Rapid tooling: Injection molding for automotive prototype tooling allows for faster production compared to traditional tooling methods. This means that automotive prototypes can be produced and tested in a shorter amount of time, allowing for quicker design iterations and improvements.
2. Cost-effective: Injection molding for automotive prototype tooling is a cost-effective solution compared to traditional tooling methods. The initial investment for the tooling is lower, and the production process is more efficient, reducing overall costs.
3. Design flexibility: Injection molding allows for intricate and complex automotive prototype designs to be easily replicated. This means that designers have more freedom to explore innovative and unique designs without compromising on functionality or performance.
4. Material selection: Injection molding allows for a wide range of materials to be used in the production of automotive prototypes. This means that designers can choose materials that best suit the specific requirements of the prototype, such as strength, durability, or heat resistance.
5. Consistency and quality: Injection molding for automotive prototype tooling ensures consistent and high-quality parts. The process allows for precise control over the molding parameters, resulting in uniform parts with minimal variations.
6. Scalability: Injection molding for automotive prototype tooling is a scalable solution, meaning that it can be easily adapted for mass production if the prototype design is successful. This allows for a smooth transition from prototype to full-scale production.
7. Time and resource savings: Injection molding for automotive prototype tooling eliminates the need for manual labor-intensive processes, such as machining or assembly. This saves time and resources, making the production process more efficient and cost-effective.
8. Durability: Injection molded automotive prototypes are highly durable and can withstand the demanding conditions of real-world testing. This makes them suitable for various automotive applications, including functional testing and performance evaluation.